Best Before Dates & Chinese Herbs
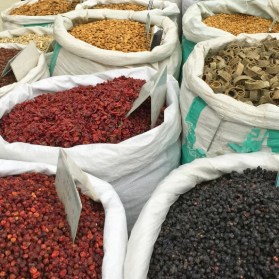
As announced in Yvonne Lau’s letter in this issue of the Mayway Mailer, Mayway is discontinuing the use of Expiration or Best Before Dates for its 5:1 extract powders. In this article, I want to provide some of the background information that led Mayway to make this decision.
Understandably, over the years, many of our customers have asked, “How long are your Plum Flower® herbs good for?” In mid-2010 in response to customer requests, Mayway began using a BBD on our raw herbs and raw herb powders. We decided that our standard procedure would be to assign five years as the Best Before Date. This dating was based on our empirical knowledge of the Chinese herb market and five years was the established shelf life of our teapills, tablets, and capsules.
Besides, we have tested and retested many of our herbs and extract powders over the years, and have found that even after 5 years or more, that the product is essentially unchanged in terms of many testing parameters, including microbial load and moisture.
Although most of our herbs are packed shortly after each year’s harvest for sale during the next year, sometimes they sell out within a year and and sometimes an herb will remain in our warehouse for longer. Of course, some herbs need to be refrigerated (e.g. Bai Guo); bones, shells, and minerals remain unchanged indefinitely; and others actually are thought to improve with aging (e.g. Chen Pi).
During a self-audit process to define Mayway’s cGMP compliance, we discovered that our shelf life determinations were inadequate, and importantly, unnecessary. While the FDA final GMP rule for dietary supplements does not require the establishment of product expiration dates, it does stipulate that a company that chooses to display an expiration or best before date, on any product, is required to have scientific, stability testing results that support the published shelf life of that product. See: 21 CFR Part 111 Final Subpart E, K. Comments on Shelf Life; http://edocket.access.gpo.gov/2007/07-3039.htm.
Lacking the requisite data, Mayway quit labeling our Plum Flower® raw herbs and raw herb powders with a BBD scarcely a few months after we initiated the program. Similarly, we have tried to find a scientific rationale for a BBD for our powder extract products and have not been able to do so. Thus, the decision to discontinue labeling these products with a BBD was made.
Why can’t you just test them for shelf life?
In the side box, I have provided some detailed information about shelf life and the issues involved in establishing it.
Stability testing involves many testing parameters that need to be tested again and again over time. The purpose is to observe whether and how the product has degraded over time, both physically and chemically, and whether harmful by- products have resulted from the degradation. A scientifically accepted gauge of quality is a chemical assay, which is the qualification and quantification of one or more chemical compounds which are relatively unique to the herb, called marker chemicals.
In the case of Chinese herbs, determining shelf life is complicated since there are no established standards that signify when an herb has reached the point where the quality has been compromised. In China, the authoritative texts are the Pharmacopoeia of the People’s Republic (PPRC) and/or the Chinese Materia Medica. The monographs do not address shelf life, whatsoever. The monographs do define authenticity of species and a baseline of quality through physical characteristics, microscopic fine structure, and occasionally chemical testing including HP-TLC or more rarely HPLC. This testing primarily focuses on identification. The monographs also define proper preparation of the herbs such as drying methods or other traditional preparation techniques (pao zhi) and recommended storage conditions. One could conclude, as far as the Chinese government is concerned, that as long as the herb meets those specifications, its quality has been established.
Unfortunately, only a few herbs have defined assays in the monographs written about them that include qualitative and/or quantitative standards for marker chemicals.
Unfortunately, most Chinese herbs do not have established marker chemicals, and even for the herbs for which marker chemicals have been identified, certified reference standards for them, which would be required for testing, are difficult to obtain. Nor do we have chemical fingerprints that have been established using HPLC or Mass Spectrophotometer-Gas Chromotography (MS-GC), et al.
Even if known, the use of so-called marker chemicals presents problems as well. While they may be characteristically present in an herb, the amount of marker chemical may not be indicative of the quality of a particular batch. Marker chemicals may also not even be therapeutically active. Additionally, sometimes the way an herb is prepared may be intended to reduce a marker chemical that is toxic.
In addition, even if there were marker chemicals for each herb or formula, certified reference standards for those markers, and chemical fingerprints for those products, the instrumentation necessary and the tests themselves can prove to be very expensive. To test each of our 450 herbs and 500 extract powders in this way would be cost prohibitive and would necessitate raising our prices significantly.
In the end, a BBD placed on a product label must be supported by scientific data, reserve samples must be maintained for one year past the shelf-life date, and dating claims must be tested by either accelerated or long term studies or other methods, as described in the side box. Simply, Mayway does not have stability testing data for these products and, consequently, chooses to not make claims regarding the shelf life of the herbs and herb powders it sells.
Why will Mayway’s teapills, tablets, and capsules continue to bear a Best Before Date?
Mayway, working with our contracted manufacturers in China, has created specifications for our teapill, tablet, and capsule products that include packaging that is impermeable to oxygen and water vapor, opaque to reduce light transmittance, and that uses a heat and electromagnetic induction, multi-layer seal. Our partners, such as Lanzhou Foci and Guangzhou Qixing, are GMP certified pharmaceutical companies with 80-130 years of experience in making similar or identical products to our own. These companies remain confident of their shelf life determinations. They conduct on-going long-term testing and periodically retest the products to ensure that the stated specifications are within the assigned limits. Additionally, since these products are registered medicines in China, shelf life and stability testing are required for a product license.
If there is no expiration/BBD, does that mean Mayway’s herbs and powder extracts are good forever?
No, not at all. Not having a BBD merely means that we do not have enough quantitative information to support establishing a precise shelf life. More accurately stated: the shelf life of these products is indeterminate. There are no shelf life guidelines available for dried Chinese herbs that we know of. Additionally, many companies’ herbs are already many years old when they reach the US. We have seen estimates that Chinese herbs are commonly 3-7 years old before they are sold in the US. Often, they have been extensively treated with sulfur dioxide, as discussed in the side box. The use of sulfites provides the appearance of freshness, but research has shown that the highly reactive SO2 has a deleterious effect on the chemical fingerprint and reduces the availability of many of the chemicals that are thought to provide the therapeutic effect of the herbs.
So, how do I know if a product is still good?
The stability of a product is dependent upon a host of factors: the product form, the nature of the individual ingredients and their rates of oxidation, as well as the packaging and storage conditions, all discussed in the side box. However, without testing data, there is no way to accurately establish the actual shelf life of a product. It is likely that if the product physically looks, tastes, and smells as it did when you first received it, it should be fine. If the herb becomes discolored, loses its characteristic fragrance, shows signs of mold or insect infestation, becomes brittle, powdery, or clumpy, develops crystals, smells rancid, et al., then the product should be discarded. Practitioners also should store their herbs in air-tight containers and protect the herbs from light and moisture.
What is Mayway doing to ensure the quality of its raw herbs and powder extracts?
Since Mayway’s Plum Flower® herbs are not treated with SO2, we use specially designed packing to maintain the quality of our herbs. Our raw herbs and herb powders are packaged in water vapor- and oxygen-barrier, plastic pouches. The raw herbs are further protected by a combination of a vacuum-sealed inner pouch and a nitrogen- flushed outer bag. This double bagging system is sometimes called a pillow-pak and effectively secures the product from oxidation. Our extract powders are packed in opaque bottles with a multi-layer foil seal and a desiccant pack. All products are stored and shipped in opaque cartons. These packaging measures protect the herbs from heat, moisture, and oxygen, which are the principal agents of spoilage thereby promoting stability.
Mayway has established specifications for all of its products, including raw herbs and powder extracts. These specifications designate the authentic species of each herb, plant part used, processing, country of origin, harvest season, cultivated or wild- crafted, allergens, storage conditions, et al. The specifications identify the standard reference texts, the test methods and acceptable test result limits. Testing is performed to identify and authenticate species, to check organoleptic parameters, sulfur dioxide residues microbial load, heavy metals, and pesticide residues. The test results are reported in each herb and product’s Certificate of Analysis. Testing is conducted in China and confirmed by independent labs in the US. Periodically, we select products to be retested and, as a general rule, we find that the parameters that we test for remain intact for many years.
Mayway is dedicated to importing the safest and highest quality herbs and herbal products possible for our customers and their patients. And, as a part of this commitment, we intend to comply with all FDA Dietary Supplement GMP regulations.
Where can I get more information?
The Code of Federal Regulations 21 CFR Part 111 Final Subpart E, K. Comments on Shelf Life; http://edocket.access.gpo.gov/2007/07- 3039.htm.
“Stability Testing Guideline for Dietary Supplements”, January 2011, NSF Stability Testing Working Group, http://www.nsf.org/media/enews/documents/Stability_Testing_Dietary_Supplements.pdf
Eisner, Stacey, “Shelf Life Dating of Botanical Supplement Ingredients and Products”, American Herbal Products Assn., http://www.ahpa.org
Bio: Skye Sturgeon, DAOM (candidate) is the Quality Assurance Manager and Special Consultant for Mayway, USA. Skye is a core faculty member at the American College of Traditional Chinese Medicine where he is also enrolled in ACTCM’s doctoral program. Previously, Skye was president of the Acupuncture & Integrative Medicine College, Berkeley. Before making Chinese medicine his career choice, Skye was a clinical biochemist and toxicologist.
What is shelf life?
Shelf life is the length of time that products are given before they are considered unsuitable for sale, use, or consumption. It is also the recommended time that a product can be stored, unopened, during which the defined quality of the goods remains acceptable under expected climatic conditions of distribution, storage and sale. Sometimes, the storage conditions are specified such as “keep refrigerated”; “keep in a cool, dry place”; or “protect from freezing”.
Often, shelf life is differentiated from an expiration date. Usually, shelf life refers to quality, while expiration dates refer to food safety. Expired fresh food products may contain bacteria and/ or contaminants sufficient to cause illness. The expiration date of pharmaceuticals specifies the date the manufacturer guarantees the full potency and safety of a drug. After the expiration date, the drug may degrade and produce chemicals that may be non-therapeutic or toxic. Shelf life in other products is often designated by a Best Before Date (BBD) to signify that the quality remains at a specified level until the BBD. That is, a product that has passed its expected shelf life (indicated by the BBD) might still be safe, but generally, quality is no longer guaranteed.
Most shelf life dates are used as guidelines based on normal and expected handling and exposure to temperature. In general, shelf life is influenced by several parameters: exposure to light, moisture, and/ or heat; transmission of gases (including water vapor); mechanical stresses; and contamination, by things such as micro-organisms or degradation products that are created as the product ages.
What other factors affect shelf life?
Other factors that affect shelf life include:
- Ingredient stability. Depending on the nature of the chemicals within a product, the degree of stability will be different. Minerals may last for decades, while volatile chemicals may disappear rapidly depending on the type of packaging and storage condition. Some chemicals may react with other ingredients in a product, while some form degradation products over time. For example, unsaturated fatty acids become rancid when exposed to heat, light, and oxygen. This sort of chemical activity can be monitored and will be factored into any shelf life determination.
- Microbiological activity. Microbial growth is promoted by moisture, heat, and a nutrient source, particularly carbohydrates and proteins. Products that are stored in areas of high humidity (>55% RH) are particularly prone to mold growth. To combat the growth of microbes, some products are formulated with high levels of salt or sugar, high or low pH, or with relatively high levels of alcohol. Additionally, many products may be subject to various levels of heat in order to reduce the microbial load at the outset and to make the product as dry as possible. With liquid products, normal or Ultra High Temperature (UHT) pasteurization may be used to reduce the plate counts of bacteria.
- Use of Preservatives and Anti-oxidants. Some products have ingredients added to their formula to lengthen the shelf life. Ingredients such as Butylated hydroxyanisole (BHA) and butylated hydroxytoluene (BHT) may be included to prevent oxidation of fats. Also, vitamins C, A, or E may be added to reduce oxidative stress. Potassium sorbate, sodium benzoate, or other preservatives may be added to inhibit microbial growth. Most Chinese herb dealers treat herbs with sulfur dioxide SO2, which acts as both an anti-oxidant and a preservative.
- Packaging and storage. Choosing the best packaging for a product can affect shelf life significantly. Various factors that must be considered in packaging include:
- container wall thickness
- closure geometry and seal
- surface area to volume ratio
- headspace to volume ratio
- water vapor permeation rate
- oxygen permeation rate
- light transmittance or opacity
- Product labels should include storage recommendations based on how light, temperature, and humidity affect the shelf life of the product. These parameters are generally defined in a pharmacopeia such as the United States Pharmacopeia (USP). For example, “store in a cool or dry place”. This means that the product should be stored between 46-59°F with the average relative humidity below 40%. Companies must also examine and consider the transportation and warehousing being used throughout the distribution network before the product reaches the end user.
- Physical form of the product. Generally, products in solid form are more stable than those in liquid form. The molecules in liquids are able to move about and collide with other molecules meaning that more chemical reactions are possible. Particle size can also play a role since smaller particles have more surface area exposed and therefore have a greater tendency to degrade. Conversely, micro-encapsulation of some ingredients segregates some chemicals from others in a formula which serves to reduce chemical reactivity. Additionally, some companies purposefully formulate their products with ingredients which are present in larger amounts than the label claims. In this way, the amount of an ingredient, even with degradation over time, will remain at the label specified level during its stated shelf life. For example, if a company knows that a product’s marker chemical or stated ingredient is reduced by 10% over its five-year shelf life, they may use 110% of the ingredient at the outset, so that, even after five years, there is still 100% of the amount of that ingredient claimed on the label. This technique is called overage.
How is shelf life measured?
All shelf life testing should be undertaken using defined specifications. These specifications should include the: (a) test parameters to be performed; (b) acceptance criteria/ values for each item tested; and (c) appropriate and scientifically valid analytical procedure to be used for each test item.
Several tests and examinations exist, which may be relevant in establishing a product’s shelf life.
- Organoleptic testing. Organoleptic properties are the aspects of a product that can be experienced by the senses, including its taste, color, smell, and/or texture. Using organoleptic testing one can compare the general appearance of a product over time. An aged product may show signs of deterioration from a freshly-made product. A good example is checking for the smell of rancidity, which means the product will exhibit a characteristically disagreeable odor, indicating the decomposition or oxidation of fatty acids or other lipids in the product.
- Closely related would be obvious physical attributes of the product. Examples would include: changes in moisture content, which may promote the growth of bacteria or molds; disintegration of pills, tablets, and capsules; clumping or caking of powders and granules; liquids may exhibit a change in pH, clarity, or viscosity, a precipitate may form, or there may be a phase separation evident; or there may be a change in the package integrity or the closure system including seals, when used.
- Microbiology. The microorganisms relevant to establishing a product’s shelf life depends on the type of product, the packaging, and the climatic conditions under which it is stored. Shelf life specifications for most products typically include microbiological testing for total aerobic bacteria (standard plate count), yeasts and mold, and selected human pathogens including coliform bacteria (such as E. coli), Salmonella, Staphylococcus, et al., as appropriate. A comparison between the microbiology test results obtained when the product is initially packaged and at defined intervals afterward will demonstrate if deterioration due to microbial activity occurs over time.
- Qualitative Chemical tests. The use of specialized analytical techniques such as high performance thin layer chromatography (HP-TLC), high performance (sometimes referred to as high pressure) liquid chromatography (HPLC), and infrared spectroscopy (IR), or other spectroscopic analysis of complex materials can give a useful representation of a product’s chemical composition. These are sometimes referred to as a chemical profile or fingerprint of the product. Changes in the fingerprint over time may be indicative of product aging.
- Quantitative chemical tests. Product quality is often based or monitored by a quantitative determination of some parameter such as the concentration of the individual drug or chemical, or in the case of herbs, a so-called marker chemical that is known to be found in the herb. This is especially important when a chemically-defined component of the product is claimed on the label. The FDA requires most foods and dietary supplements to provide at least 100% of their claimed component levels throughout the shelf life, although there are exceptions to the rule. Nonetheless, the level of the claimed component can be tested at multiple intervals in order to verify that the product maintains an appropriate level of that component throughout the labeled shelf life. This same method is used by some companies even when no quantitative label claims are made. HPLC and Gas Chromatography (GC) may be used for quantitative testing.
Other methods for obtaining shelf life data
When shelf life dating is used, a company must create or acquire data to support the shelf life claim. In addition to the methods described above, several other techniques may be used. These include:
- Information from the public domain. Some products have been extensively researched and the results have been published. So long as a company packages and stores a product in a similar manner as that in the published data, the shelf life can be inferred to be relativity the same as that indicated in the research.
- Manufacturer’s knowledge. Similarly, when ingredient manufacturers have accumulated data over numerous batches of the same product, shelf life can be approximated based on their internal empirical data.
- Long-term testing. Also called “real time” testing, this is often used to determine the initial shelf life data. A company continues to test samples that have been kept under the label-specified conditions until obvious deterioration of the product becomes evident.
- Accelerated or stress testing. This type of testing is used to gain predictive information about a product in a relatively shorter amount of time than real time testing. It is used to determine a material’s susceptibility to degradation caused by elevated temperature, humidity, light, acidic or basic conditions, and/or oxidizing or reducing substances. By stressing the product with higher heat, etc. a company can approximate the conditions that would occur over a longer period. This sort of testing must be confirmed by long-term testing to be 100% valid.
- Periodic retesting of product reserve samples or products remaining in inventory. Since cGMPs require the retention of samples from each batch/lot of product that is produced, this is a good source for retesting of product. Alternatively, a company can cull from inventory samples for retesting.